What are Cast Wheels?
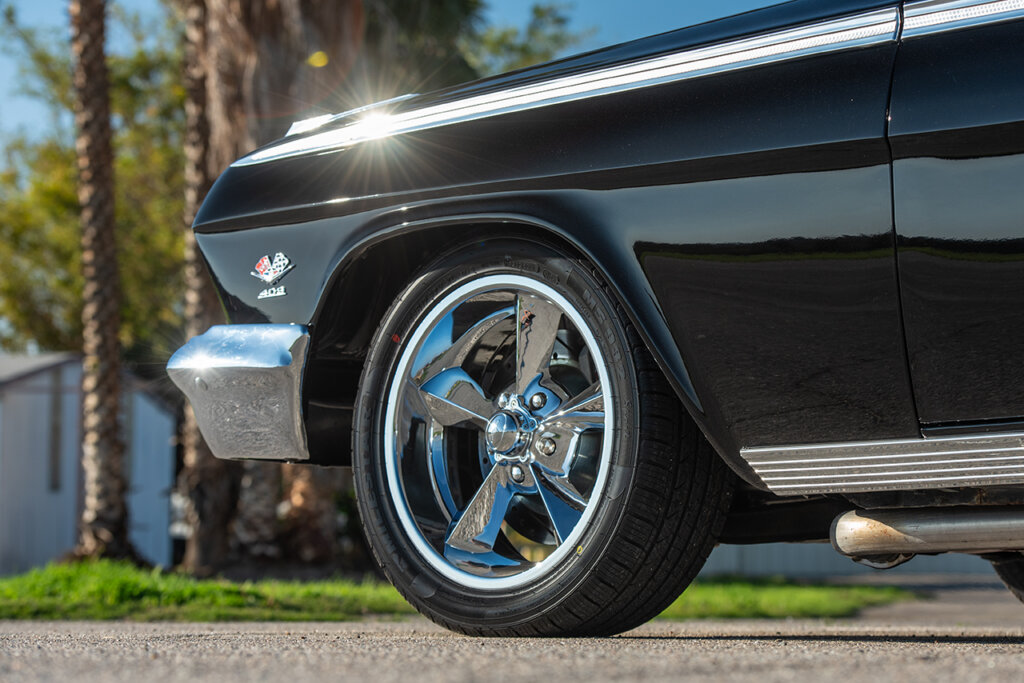
Source: Motofutura
How cast wheel production starts is by first melting down material. The molten metal is poured into the mold cavity, occupying the space left behind by the pattern. As the metal cools and solidifies within the mold, it adopts the wheel’s intended shape. Once the solidification process is complete, the mold is opened, and the cast wheel is extracted. Any excess material, as well as the pouring channel (sprue), are subsequently removed.
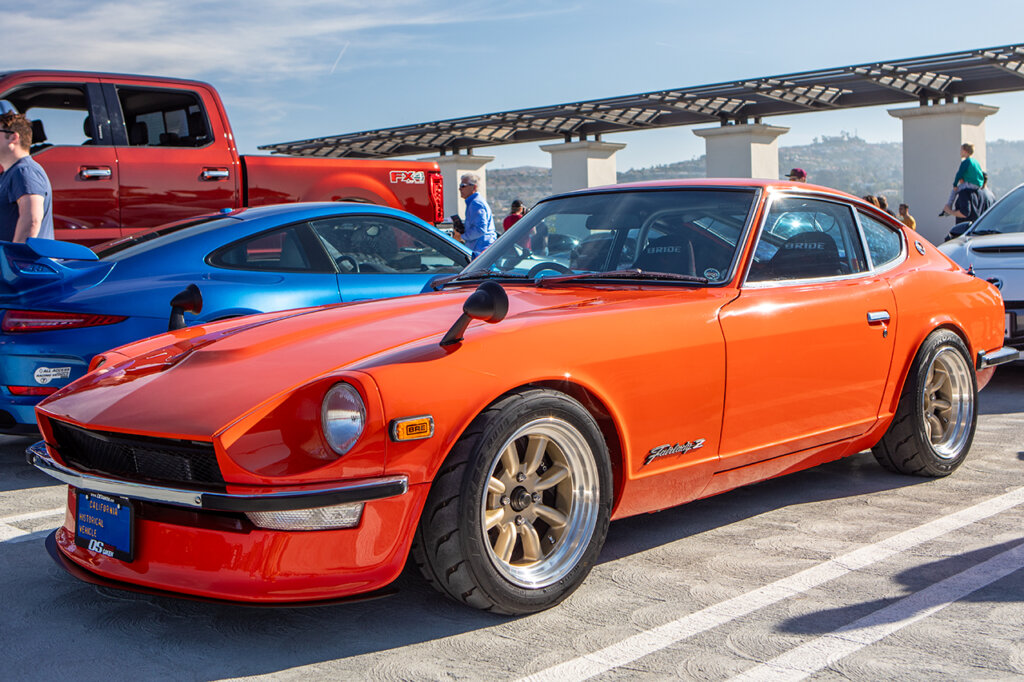
Source: Motofutura
Subsequent stages involve finishing and machining the casting. This entails cleaning the casting and addressing any imperfections present. Precision is achieved through machining processes, ensuring accurate dimensions, smooth surfaces, and the incorporation of attachment points. Surface finishing is an additional step, where the cast wheel undergoes treatments such as painting, powder coating, or polishing to achieve the desired aesthetic appearance.
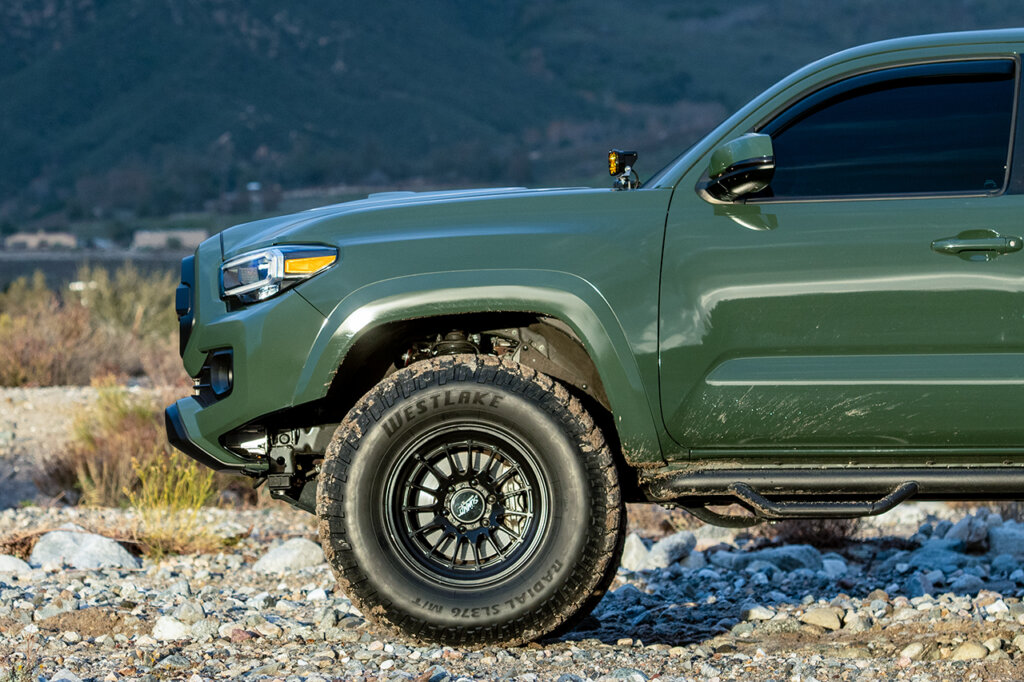
Source: Mototfutura
Advantages associated with cast wheels include their design flexibility, enabling intricate and complex designs that may be challenging to produce using alternative manufacturing methods. Additionally, the casting process is cost-effective for large-scale production, making it a suitable choice for bulk quantities of wheels. The method is relatively swift once molds are prepared and offers the potential for wheels with good strength characteristics. Furthermore, cast wheels can be finished in various ways to attain desired aesthetics.
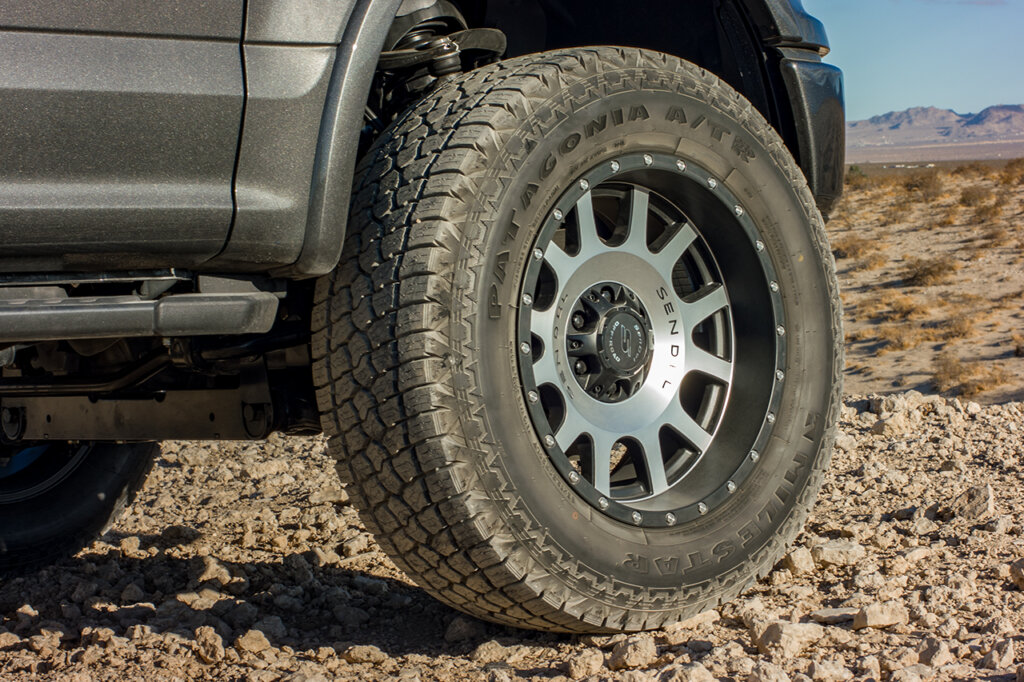
Source: Motofutura
Conversely, cast wheels also exhibit certain drawbacks. They tend to be heavier than alternatives like forged wheels, which can impact vehicle performance in terms of acceleration, braking, and fuel efficiency. Additionally, the casting process might lead to minor variations in dimensions and surface quality compared to more precise manufacturing methods like forging. Cast wheels may possess lower strength compared to forged wheels, which could result in concerns during high-stress situations. The casting process could also introduce porosity (air pockets) within the metal, potentially affecting structural integrity. Moreover, cast wheels might not offer the same level of heat resistance as forged wheels, which could be problematic in high-performance or racing applications.